by summer
Share
What is Pallet Racking System?
A pallet racking system is a specialized racking system for storing pallets of goods, which is a material handling storage aid system. Most pallet racking is designed to store heavy loads, usually with a load capacity of 1000kg to 3000kg per level, and custom heavy-duty pallet racking with a load capacity of even 5000kg per level.
Various types of racking have been developed depending on storage requirements and access methods. Although different pallet racking types are used in different scenarios, the racks are designed to meet industry standards, and industrial storage racks, forklifts, and other storage and handling equipment are designed to meet these standards.
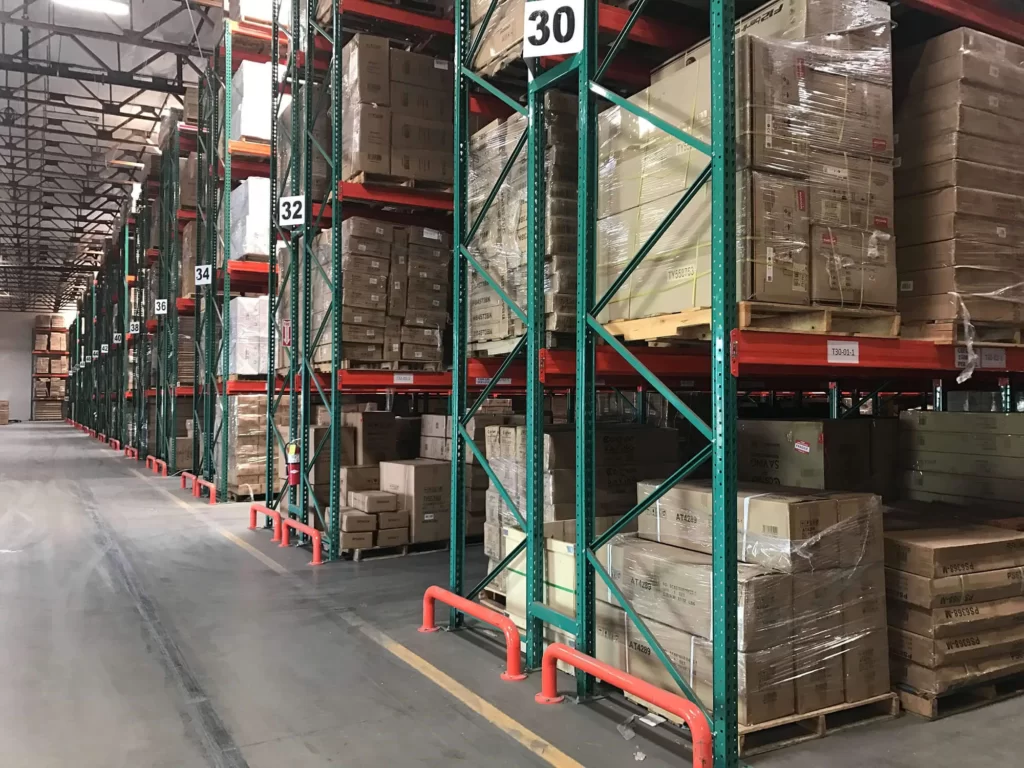
The main structure of the pallet racking is an upright frame and beams, and the ends of the beams are welded with a hanging clasp, and the clasp is embedded in the holes reserved for the upright, and safety pins are inserted. The pallet racking structure is relatively simple, the cost is relatively low, easy to install, which also makes it the most widely used warehouse storage rack.
Pallet racking can significantly improve the space utilization of the enterprise’s warehouse, at the same time, the use of pallets loaded goods greatly improve the efficiency of storage and can save a lot of storage costs for enterprises, pallet racking is an indispensable storage tool in the storage process of modern enterprises.
To learn more about what is a pallet rack please read what is a pallet rack, this article will explain this issue in more detail.
Benefits of Pallet Racking.
The low cost and practicality of pallet racking make it the most important component of a warehousing project. Since many business owners do not understand the knowledge related to the warehousing industry and have not purchased warehouse pallet racking, many companies still have large areas of underutilized storage space in their warehouses, and the use of pallet racking is the ideal solution to maximize the use of warehouse storage space and reduce the waste of storage space. Pallet racking systems can solve many warehouse storage-related problems, the advantages of pallet racking can be summarized as follows.
- Easy access, reduced access time, and improved access efficiency.
- Used in conjunction with labels, picking errors can be reduced.
- Maximize the use of warehouse space, saving storage costs for the company.
- Anti-rodent and moisture-proof, safer storage of goods.
- Transport and handling are more flexible and convenient.
- The inventory quantity is simple and clear, and the control of inventory is more controllable.
- Reduce clutter, a clean and tidy warehouse can enhance your corporate image.
What are the main types of pallet racking?
Pallet racking is widely used around the world, but not all pallet racking systems are created equal. There are several types of racking to choose from and they are designed for different application scenarios. For example, some types of pallet racking are designed to provide a dense storage capacity that maximizes the use of storage space, while other types of racking are designed to achieve greater storage efficiency, allowing for easy access to goods in each storage bay. To help you understand how to choose the right pallet racking for your warehouse, below we will describe the characteristics of the different types of pallet racking and their corresponding application scenarios so that you can find the right type of racking for your warehouse and goods, and thus develop the optimal storage solution.
1. Selective pallet racking system
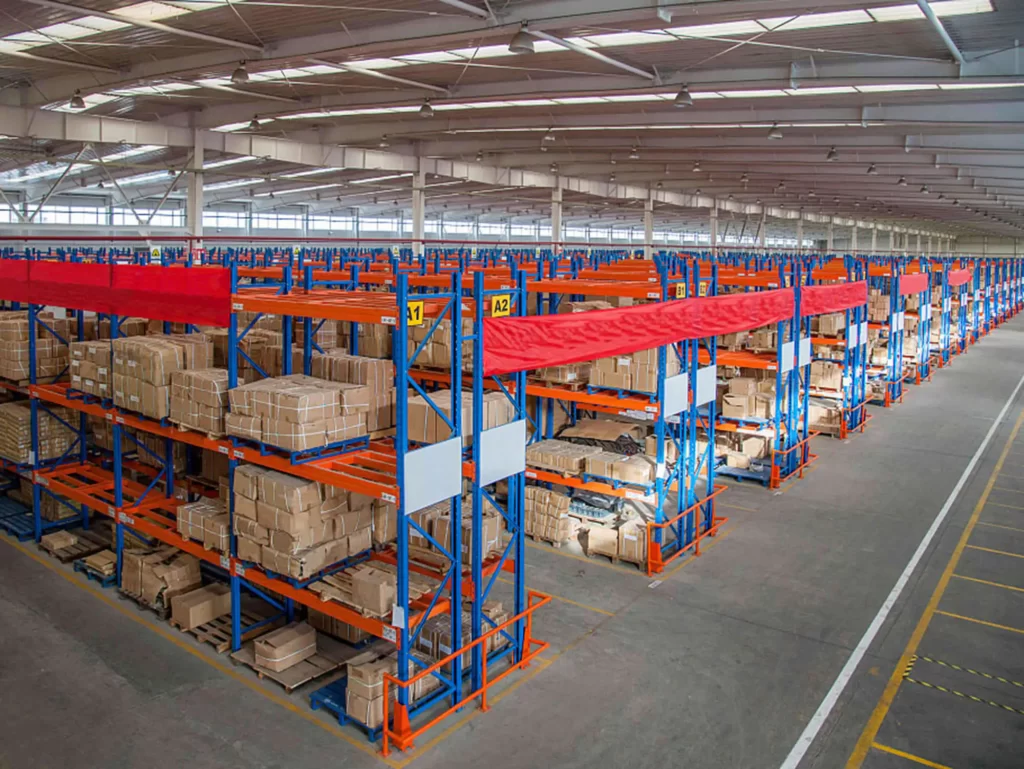
Features of selective pallet racking:
The reserved aisle is larger, usually greater than or equal to 3.6 meters, which is convenient for the counterbalanced forklift to access the goods.
It is a first-in-first-out storage method.
It is the most common type of racking.
The goods can be accessed at any time in any storage position.
The total height of the rack usually does not exceed 10 meters.
Warehouse space utilization is about 30%.
When to use it?
When the amount of goods you need to store is relatively small.
When you want to access any storage space at any time.
When your warehouse is not too high.
When not to use it?
When you need to store more goods and need a more dense storage racking system.
When your warehouse is very high and you want to maximize the use of your warehouse space.
The advantage of selective pallet racking.
2. Narrow aisle pallet racking system

Features of narrow aisle racking:
Set up with 1.6 to 2 meters of aisle access.
Requires a special narrow aisle forklift.
First-in, first-out storage method.
Access to any storage position at any time.
The narrow aisle forklift moves in a straight line along the floor guideline.
The height of the racks is high, usually over 6 meters.
Warehouse space utilization is about 65%.
When to use it?
When you have a large number of cargo categories and a relatively small amount of cargo in each category.
When you have a narrow aisle forklift or you plan to purchase a narrow aisle forklift.
When the turnover rate of your goods is high.
When you want to access the goods in any storage position at any time.
When you have a high warehouse height and you want to maximize the space utilization of your warehouse with a limited budget.
When you can’t use it?
When your warehouse does not have a narrow aisle forklift and you have no plans to purchase one.
When you are looking for higher utilization of warehouse space.
When your warehouse height is low.
When you have an uneven warehouse floor.
3. Double-deep pallet racking system

Features of double-deep pallet racking:
Set a 3-meter of access to pass.
First-in, last-out storage method.
Four sets of pallet racks in each row are connected back to back.
Access work must be done with a deep-reach forklift.
Warehouse space utilization is about 42%.
When to use it?
When you have a deep-reach forklift in your warehouse or you plan to purchase a deep-reach forklift.
When you need to maximize the utilization of your warehouse space with a limited budget.
When you have fewer categories of goods and a larger quantity of goods.
When you are storing goods with a long shelf life that allows for first-in, last-out storage.
When you can’t use it?
When you do not have a deep-reach forklift or do not plan to purchase a deep-reach forklift.
When you need to access any storage space at any time or frequently.
When you have a large number of goods and a small number of individual goods.
When you store goods with short shelf life and need to use the FIFO storage method.
4. Drive-in pallet racking system
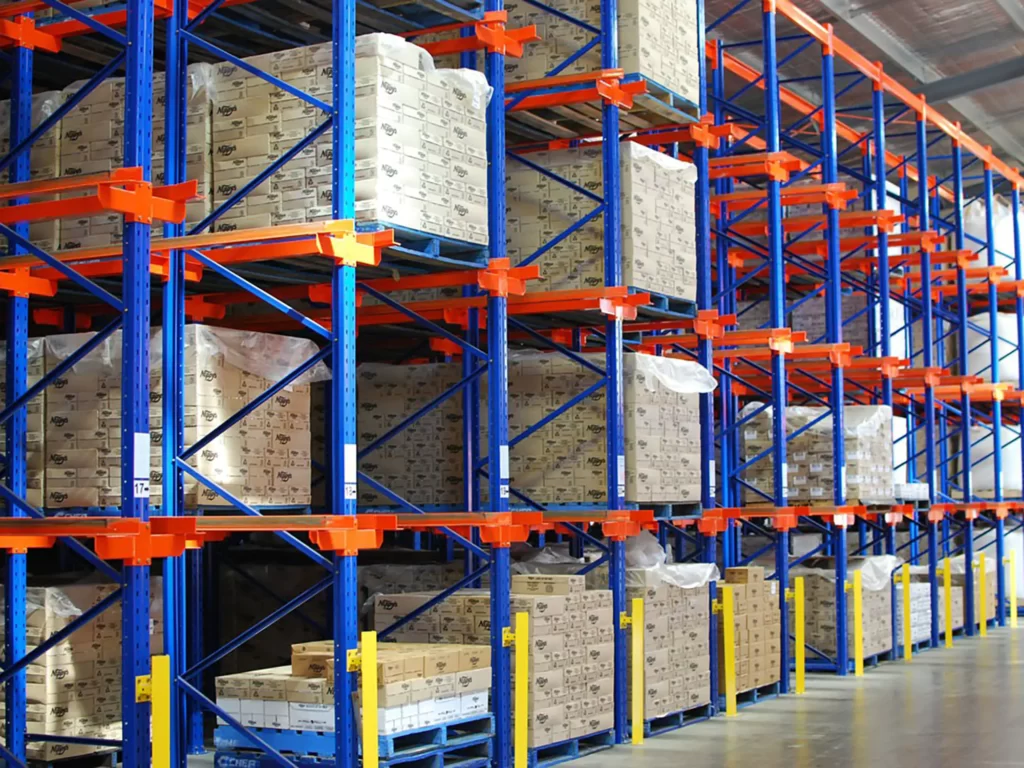
Features of drive-in racking:
The 3.6m aisle is convenient for a counterbalanced forklift or forklift to access the goods.
The first-in, last-out storage method is suitable for storing goods with long shelf life.
Rack height usually does not exceed 10 meters.
Forklift trucks are driven inside the racks to access the goods.
The depth of the rack can be 10 to 12 pallets and the height of the rack can be 3 to 7 pallets.
Warehouse space utilization is about 70%.
When to use it?
When the goods have a long shelf life and low turnover.
When goods are allowed to be stored in a first-in, last-out method.
When the type of goods is small and the number of goods to be stored is large.
When you want to increase storage density and pursue higher space utilization.
When you do not need to access the goods at any storage location at any time.
When you can’t use it?
When you need to have access to goods at any location at any time.
When you store goods that do not support the first-in, last-out storage method.
When there are many types of goods stored and the number of goods of each type is small.
What is drive in racking and how to use and maintain it?
5. Radio shuttle racking system (shuttle racking, Satellite Racking)
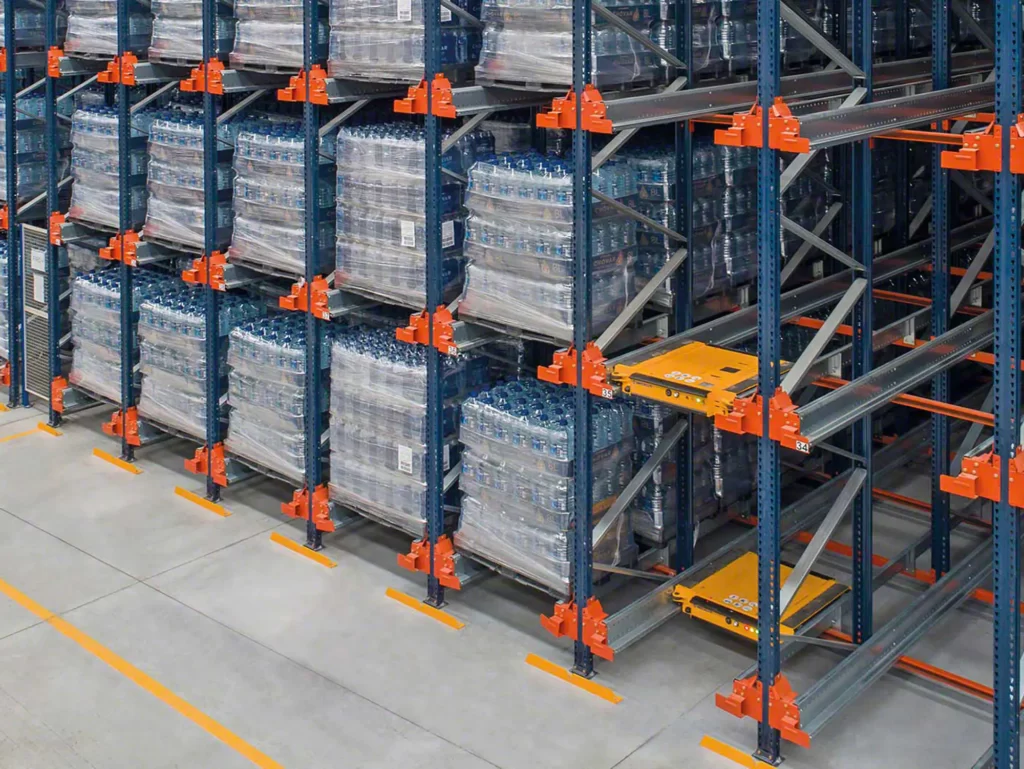
Features of shuttle racking:
Aisle of about 3.6 meters for forklifts.
The goods are placed at the pick-up point by forklift and then transferred to the designated storage location by pallet shuttle.
Each track is usually set up with 10 to 40 pallet positions.
Pallet shuttles are moved to different tracks with forklifts.
FIFO or FILO storage method is possible.
Warehouse space utilization is about 80%.
When to use it?
When the stored goods have a high turnover rate and are in and out of storage frequently.
When the stored goods need to be stored using the FIFO storage method.
When you want to automate your storage system and reduce labor costs.
When you want to maximize the use of space and pursue the ultimate space utilization.
When not to use it?
When your warehouse is small and the number of goods stored is small, the cost of pallet shuttle is relatively high.
When your budget is low. This type of racking is much more expensive to manufacture than regular racking.
When you have an uneven floor. The stable operation of the pallet shuttle requires high precision of the racks, rails, and floor.
The advantages of shuttle racking.
6. Gravity flow racking system

Characteristics of gravity flow racking:
About 3.6m aisle for the forklift to transfer goods.
First-in-first-out storage method is used.
The pallet with goods is placed on the rolling track at the entrance of the racking by forklift, and the pallet will automatically move slowly to the pick-up port due to the self-weight of the goods.
The racks should not be too high, generally within 6 meters.
The rack as a whole is inclined at 3 to 5 degrees
Warehouse space utilization is about 75%.
When to use it?
When you store goods that need to be stored in a FIFO storage method.
When you store goods with a high turnover rate.
When you want to reduce the cost of manual picking.
When you want to increase storage space utilization.
When not to use it?
When the floor of your warehouse is not very flat.
When you need to perform picking operations on goods.
When you need to store a large variety of goods and a small number of goods.
7. Push-back pallet racking system
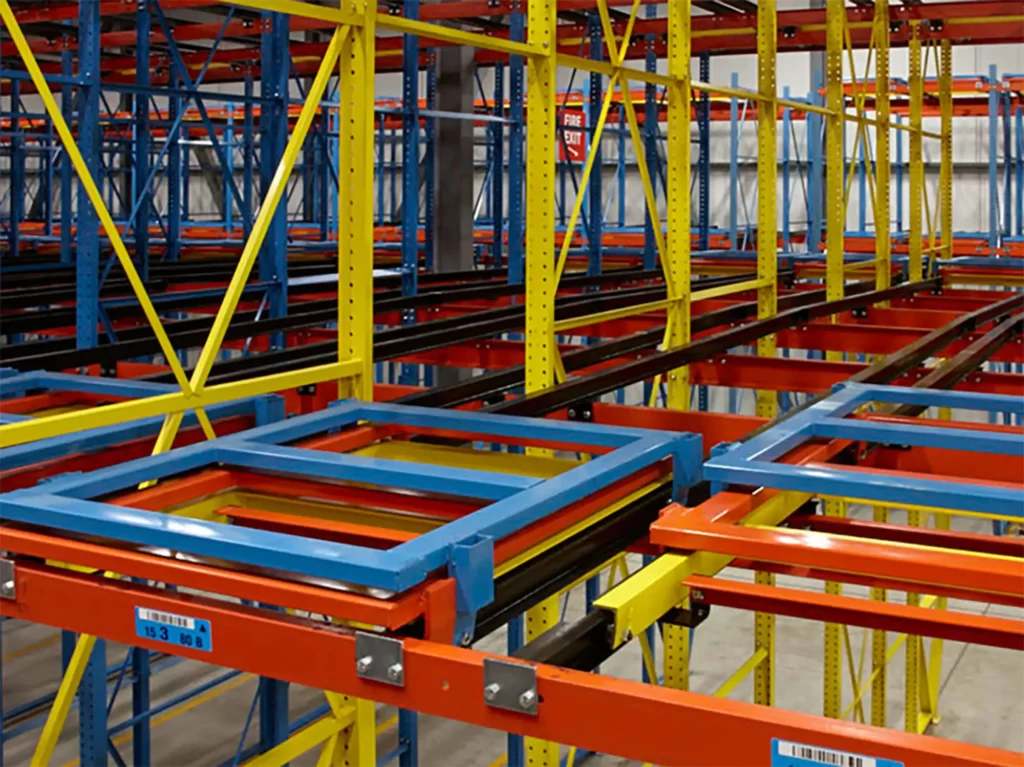
Features of push-back racking:
Last-in, first-out storage method
Depth is usually three pallet positions, less than four pallet depths.
By forklift truck pushing the goods on a pallet position in front to make them reach the designated storage position.
Pallets with goods are placed on movable trolleys by forklift.
Warehouse space utilization is about 60%.
When to use it?
When the type of goods you need to store is large and the number of goods is small.
When you are storing goods with long shelf life and the first-in, last-out storage method is applicable.
When you do not need to pick up goods at any location.
When not to use it?
When you need to perform picking operations for goods on an order.
When you need to store goods to meet the FIFO storage method.
When your products are fragile and pushing is more likely to cause damage.
What is push back racking?
8. ASRS (Automated storage and retrieval system)

Features of ASRS:
Less than 2m aisle for stacker crane movement for cargo access.
Automated storage and retrieval system controlled by a computer system
High rack height, usually more than 10 meters, storage density is extremely high, which can maximize the use of warehouse space.
Warehouse space utilization is more than 90%.
When to use it?
When you want to use the storage space to the maximum.
When the turnover of goods is very high you can choose ASRS.
Choose it when your budget is sufficient.
When you want to automate your warehouse storage ASRS is the better choice.
You should choose it when you want to pick up goods at any location at any time.
When not to use it?
You can’t choose it when you have a limited budget, ASRS is very costly.
You don’t need to consider it when your warehouse is small and the amount of goods to be stored is small.
You can’t choose it when you don’t have a developed warehouse storage management computer system.
What is ASRS Racking?
How to design an automated storage and retrieval system?
Pallet racking main structure and accessories.
1. Pallet racking upright: upright is the vertical support in the pallet racking system, which consists of two uprights connected by bolts through horizontal and diagonal bracing to form the upright frame. The holes on the upright column are spaced 75mm apart, which can support the beam to adjust the height and number of layers up and down with a spacing of 75mm.
2. Pallet racking beam: The pallet racking beam is the horizontal support in the pallet racking system. The beam is welded with a hanging clasp at both ends, which can be easily embedded into the holes of the upright, and the beam is connected to the upright frame to form a whole frame to play a solid role. The beams are available in various sizes and thicknesses, depending on the load capacity and the size of the pallets stored, and are usually set at 2700mm long for two pallets per level. Pallet racking with step beams or box beams, equipped with support beams or wire decking will be safer to use. Holes are reserved on the hanging clasp of the beam for installing safety pins. The beam with safety pins installed is not easy to fall off, which improves the safety performance of the pallet rack.
3. wire mesh decking: wire deck is a mesh deck made of welded wire, the mesh is usually 50 * 50mm or 50 * 100mm two options, wire deck bottom is welded with four reinforcing ribs, both sides bent on top of the beam of the rack when the goods are not used pallets and placed directly on the rack storage will not fall, helping to prevent goods from falling from a height to occur It helps to prevent cargo from falling from high places and effectively protects the personal safety of warehouse workers. The metal wire deck is available in galvanized and powder-coated finishes for you to choose from.
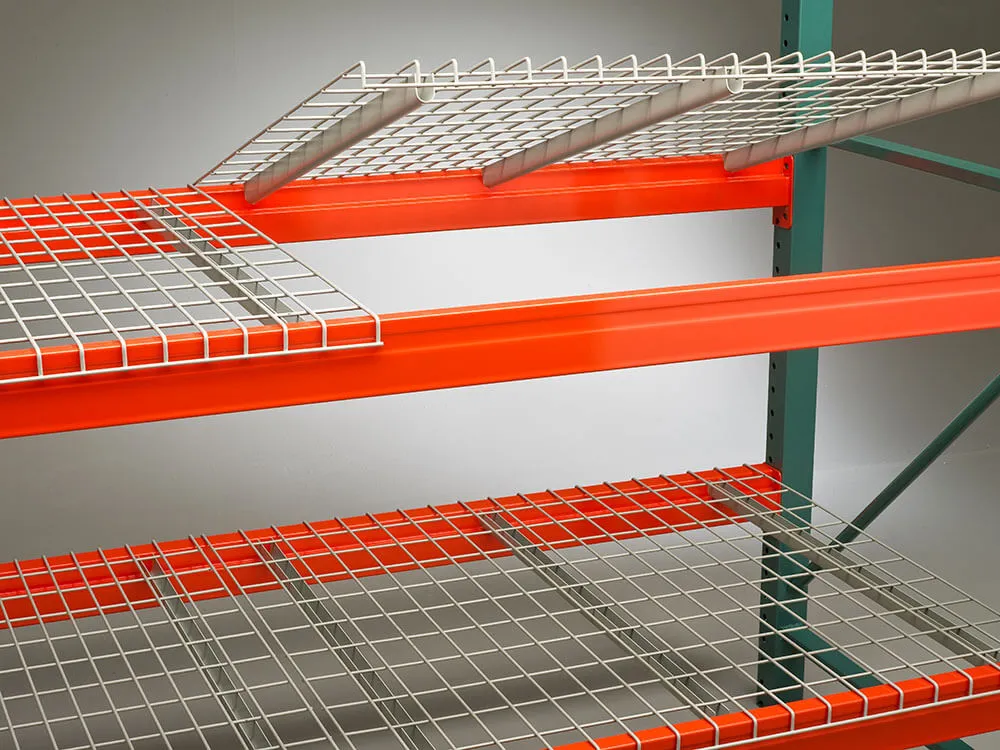
4. Pallet rack upright protector: upright protector can effectively protect the rack upright from forklift impact or reduce the damage caused to the upright due to forklift impact, thus avoiding serious safety accidents such as deformation of the rack or even the collapse of the rack. Rack upright protectors are made of plastic and steel, plastic upright protectors are affordable and practical, and steel upright protectors are stronger and more durable and can be reused.
5. Support beam: The support beam spans across the rack beam, further enhancing the stability of the rack. Usually, each layer is equipped with five support beams, often used in conjunction with the plywood, which can improve the bearing capacity of the plywood.
6. Row spacer: row spacer is used to connect one set of racking systems with another set of racking systems parallel to it, which helps to improve the stability of the racking system.
A pallet rack consists of a starter bay and an add-on bay, usually, the first set of the rack at the end is the starter bay, and each set of racks added later will share the upright frame with the previous set of racks, the such rack is called add-on bay, so the difference between starter bay and add-on bay is that starter bay has one more upright frame than add-on bay. Generally speaking, the starter bay plus add-on bay structure is more stable and safe than the single starter bay structure, and the starter bay plus add-on bay structure can save you more cost because the add-on bay has one less upright frame.
Pallet racking installation.
Different types of racking are installed in different ways, whether the pallet racking is installed correctly will directly affect the efficiency and personal safety of warehouse workers, so the pallet racking installation needs to be carried out by professional racking installers, properly installed pallet racking should be free of any safety hazards and is practical.
In addition to manufacturing a variety of warehouse storage racks and warehouse handling equipment, Mracking has trained many well-trained rack installers who specialize in pallet rack installation, rack repair, and structural steel mezzanine installation and disassembly. Mracking can provide you with thoughtful rack installation services to ensure your safety and practicality during the use of the racks, contact now Mracking for racking installation support now.
Considerations for choosing a warehouse racking system.
Before designing a pallet racking system, the factors you need to know include warehouse dimensions, the total number of pallets, weight per pallet load, pallet size, type of forklift, and FIFO or FILO storage method.
Warehouse dimensions: It is best for you to have a clear layout of your warehouse, including parameters such as the length, width, height, and location of wall columns, so that you can plan clearly when designing your racking system, avoiding obstacles as well as designing the right height of the rack. Reasonable design to maximize the use of storage space.
Total number of pallets: The number of pallets that need to be stored in the whole racking system. Make a clear count in order to confirm the number of racks needed.
The load capacity of each pallet: Calculate the load capacity of each pallet to determine the load capacity of each level of the racking system. Take selective pallet racking as an example, usually, two pallets are placed on each level, if the load capacity of each pallet is one ton, then the load capacity of the racking should be designed to not be less than two tons per level.
The size of the pallet: the size of the pallet will directly affect the design of the length and width of the racking. Taking the standard 1200*1000mm pallet as an example, no additional space is needed except for the 100mm safe operating space between the rack upright and the pallet and pallet in advance, so the length and width of the pallet racking will usually be set at 2700mm and 800mm.
Whether the stored goods are perishable or not: If the stored goods are food products with a short shelf life, the good’s turnaround time needs to be taken into account in the design, and the racking system with the FIFO storage method is preferred.
Type of forklift: The type of forklift is also something you need to consider. What type of forklift is being used in your warehouse or do you have plans to purchase a new one? Different racking systems use different forklifts. For example, narrow aisle racking systems require narrow aisle forklifts; double deep racking systems require articulated forklifts; and selective racking systems simply require regular forklifts.
FIFO or FILO storage method: Different racking systems use different access methods, so the turnover efficiency is different. For goods requiring faster turnover efficiency or shorter shelf life, you should choose the FIFO racking system; for goods with longer storage periods and longer shelf life, choosing the FILO shelving system is appropriate, which will save your storage cost.
Pallet racking identification.
Teardrop pallet racking system.
Teardrop pallet racking is called because of the “teardrop” shape of the holes in the upright. Teardrop pallet racking is a common type of racking in the American market, including the United States, Brazil, Mexico, Canada, and other American countries.

Diamond hole pallet racking system.
The diamond-shaped hole pallet rack is named after the “diamond” shape of the hole in the upright. This type of hole pallet rack is mainly made in China and is widely used in China. At the same time, because Chinese rack manufacturers export a lot to some countries in Southeast Asia, you can also easily find this type of hole pallet rack in the Southeast Asian market.
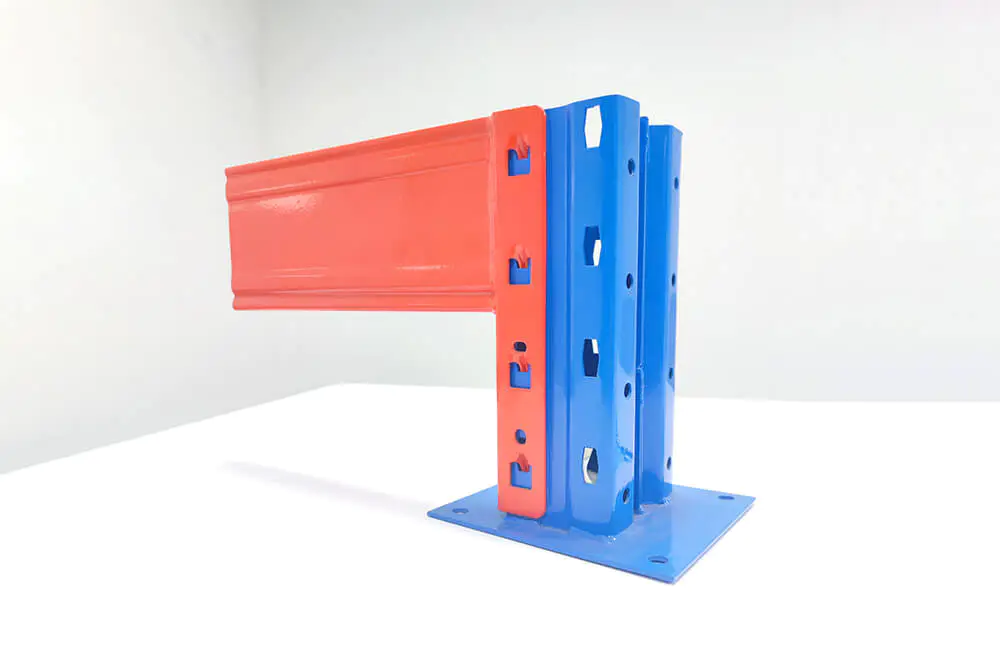
Adjustable pallet rack system.
The height and number of levels of adjustable pallet racks can be adjusted arbitrarily to meet storage needs. Most pallet racking is of assembled construction, which means you can easily adjust it to fit your warehouse and meet your actual storage needs.
Mobile Pallet Racking System.
Mobile pallet racking is electronically driven with bottom-mounted rails that are controlled by a computer system that allows for full-row movement. Goods can be accessed at any time in any pallet position, but mobile pallet racking is expensive and unnecessary for most businesses.
Other types of warehouse racking.
1. Cantilever racks system.
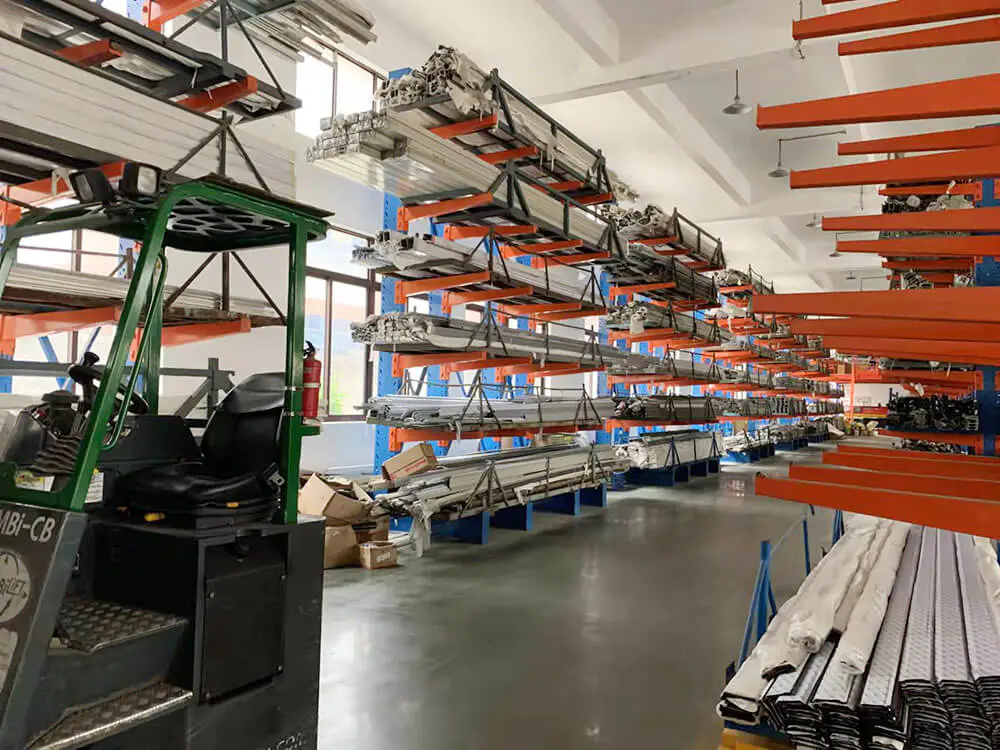
Cantilever racks consist of columns, bases, arms, and rods. Cantilever racks are mainly used to store long materials, pipes, plates, and irregular goods, and are often used in the machinery manufacturing industry or building materials supermarkets. After loading the panel, pallets can be used for storage. Cantilever racks are very suitable for warehouses with small spaces and low heights, and their space utilization rate is higher than ordinary racks.
2. Mold racks system.
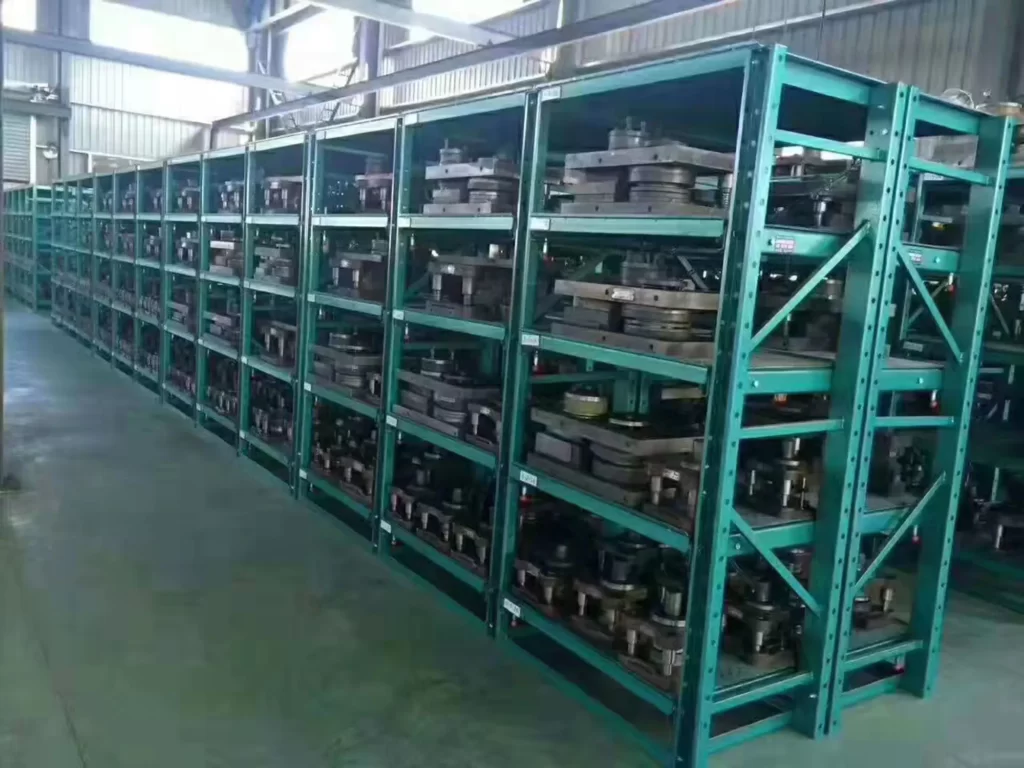
Mold racks are mainly used to store injection molds, hardware molds, die-casting molds, etc. Equipped with a traveling crane at the top, it can easily realize the lifting of molds. Sliding rails are installed on both sides of the drawer panels, and the drawer panels can be pulled out, making the access to molds very convenient. The standard mold rack size is L3100*D600*H2000mm, and the load capacity is 1000kg per drawer panel.
3. Mezzanine racking system.
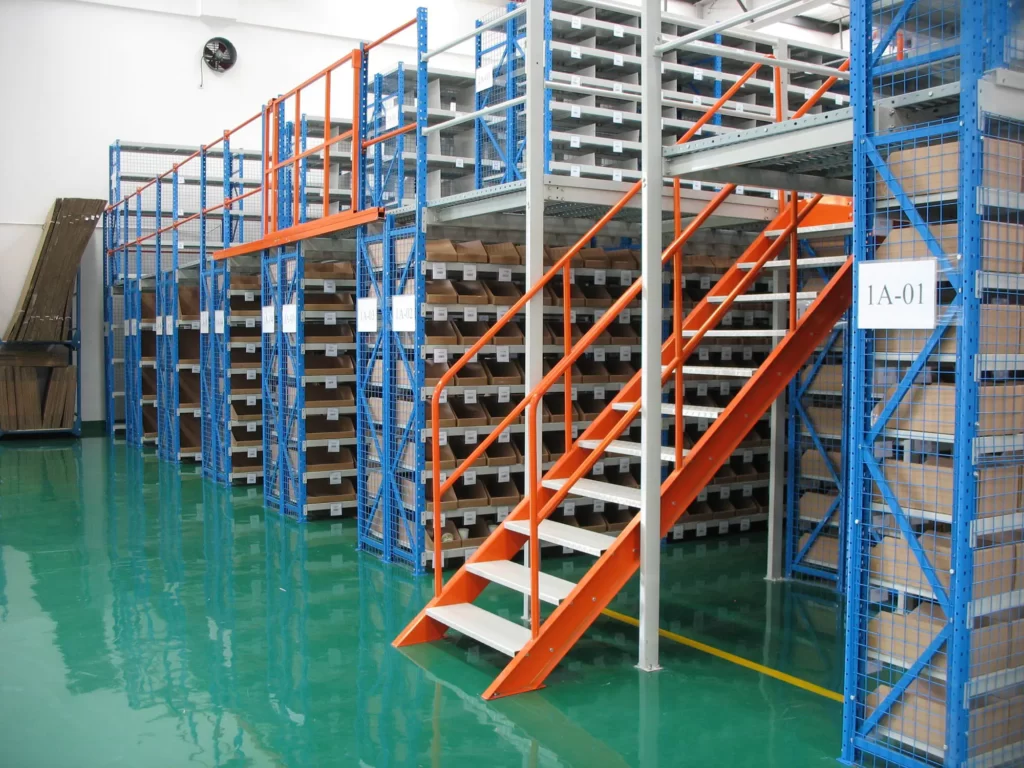
Mezzanine racking is a mezzanine racking system using a pallet rack as support plus a mezzanine floor, also often called pallet rack mezzanine or rack supported mezzanine floor. mezzanine racking has a very high storage density and is suitable for storing relatively light and small goods, usually using manual access operation. It can be used with pallet trucks, hydraulic lifts, elevators and other tools to improve access efficiency.
4. Boltless racking system.
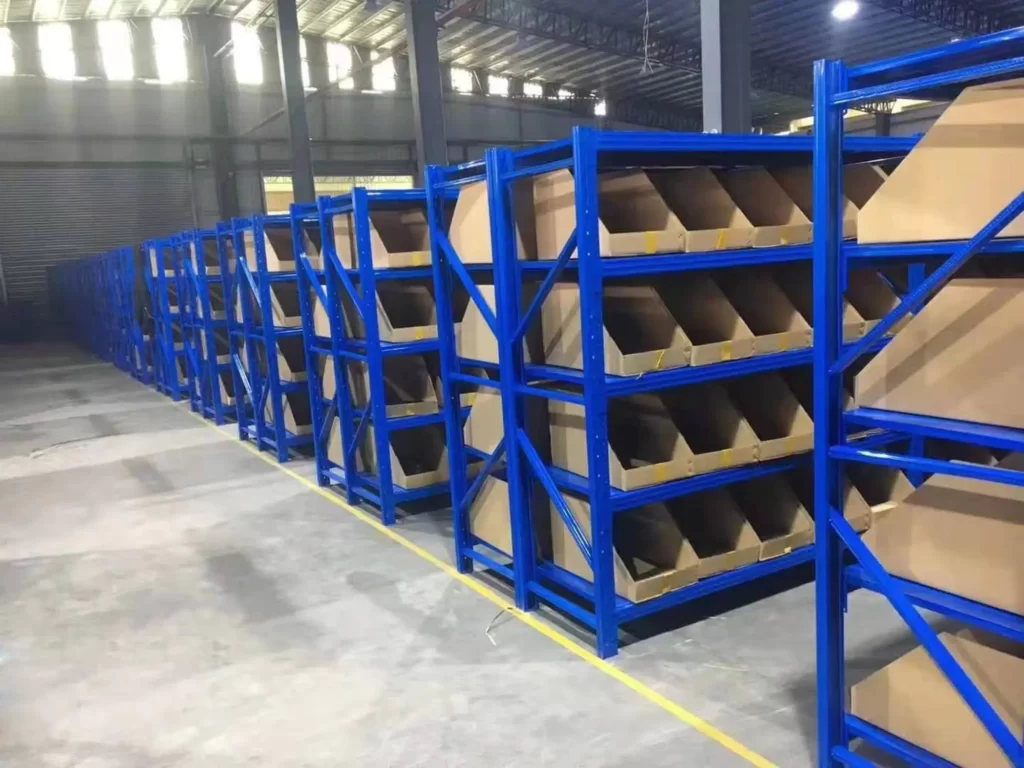
Boltless racking belongs to light storage racking, with a load capacity usually in the range of 100-500kg per level, with steel panels laid on the level, and relatively easy to install. Boltless racks are suitable for storing lighter weight and smaller volume items, are suitable for manual stacking, and are more widely used in electronics, clothing, medical and food industries.
5. Stacking rack system.

A stacking rack is the handling and storage equipment derived from pallets. The stacking rack has a simple structure and can be folded, the folded volume is small, and will not take up a lot of space, but also can be stacked, very suitable for storing clothes. After installing casters, it can be used as independent handling equipment, which is very convenient and practical.
6. Carton flow racking system.

Carton flow racks are mainly composed of uprights, beams, flow strips, baffles, and picking boards. The racks are tilted at a certain angle, using the self-weight of the goods to slide down slowly, stocking them on the higher side of the aisle and picking them up in the other aisle. The common sliding containers of carton flow racks are turnover boxes, parts boxes, and cartons, which are suitable for short-term storage and picking of small pieces of goods.
7. Slotted angle steel racking system.

Slotted angle steel racks are mainly composed of upright, beams and panels, with simple structure and easy assembly. It is mainly used for storing small and light goods, with a single layer carrying a capacity of 150kg or less. It is widely used in homes, garages, supermarkets, etc. It can also be applied in warehouse storage projects and can be easily moved with the addition of casters at the bottom, which is very convenient.
From selective pallet racking with a simple structure to complex warehouse racking systems, Tuobang Racking can provide you with a range of services including design, production, transportation, installation, etc. According to your actual budget situation, we can design and develop the most suitable storage solution for your warehouse and products.
If you are worried about which pallet racking type you should choose for your warehouse, please contact us today for a free consultation to help guide you through the process of choosing a pallet racking type for your warehouse from start to finish.
If you are in the lumber business, you know that proper
If you are a fabric store owner, a quilter, or a sewing